(4)パイプは市場で流通している既成のサイズを活用する
精密板金においては、市場に流通している規格品をうまく活用することで納期短縮とコスト削減に繋げることができます。例えば上記のようにパイプ形状の物を使用する場合、市場に流通していない太さのもので設計を行うと、ステンレスなどの板から三本ロールなどで曲げ加工を行なった上で溶接をしなければなりませんので、溶接の手間とコストがかかってしまいます。
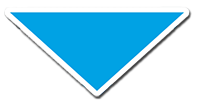
サイズ | 厚み |
---|---|
5 | 0.8 |
1.0 | |
6 | 0.8 |
1.0 | |
7 | 0.8 |
1.0 | |
8 | 0.8 |
1.0 | |
9 |
0.8 |
1.0 | |
10 | 0.8 |
1.0 | |
12 | 0.8 |
1.0 |
サイズ | 厚み |
---|---|
13 | 0.8 |
1.0 | |
1.2 | |
1.5 | |
13.8 | 1.2 |
1.5 | |
14 | 0.8 |
1.0 | |
15 |
0.8 |
1.0 | |
16 | 0.8 |
1.0 | |
1.2 | |
1.5 | |
2.0 |
パイプ形状であれば、市場に流通している規格品から選定し設計に反映させることがコストダウンにつながります。市場ではJIS 規格品よりも化粧パイプの規格品のほうが流通しているため、それらを積極的に採用し設計する方が望ましいといえます。
その他関連するコストダウン事例
-
(1)板厚はなるべく同じ厚さのものを採用する
【Before】
ステンレスやアルミなどを用いた精密板金を設計する際には、なるべく同じ厚さのもので統一して設計することがコストダウンに繋がります。上記のようなサイズのステンレスの板が必要で、板厚が2種類ある場合は、購入するステンレスの板を2 種類購入しなければならないので、仕入れコストが高くなります。さらに余分な材料まで購入することになりムダが生じてしまいます。 また、溶接を行う場合においては、特にこの板厚の違いには気をつける必要があります。一般的に薄い板の方が熱が早く伝わるため、板厚が違うと溶接不具合が発生する確率も高くなってしまいます。
→解決事例を見る
-
(2)定尺を考慮した設計でコストダウンを行う
【Before】
ステンレスや鉄などの板材は定尺と呼ばれる決まった寸法があり、市場では基本的にはそれが元となり流通しています。たとえばステンレスを使った精密板金の製品を設計する場合、ステンレスはメーター板という1m ごとに市場で流通しているので、展開寸法が1,000 × 900 と950× 900 では1,000 × 900 の方が材料費が倍になってしまいます。
→解決事例を見る
-
(3)流通性の高い材料、板厚の使用でコストダウンを行う
【Before】
機器を設計するにあたっては、求められる機能から材料を選択することが必要ですが、品質・機能とコストのバランスを取る場合には、材料のコストや入手性も考慮した上で選定を行わないとスムーズな立上げや量産を行なうことができません。例えば、チタンで精密板金の製品を製作すれば耐食性も高く軽量なので機能としては十分ですが、流通性が低く、コストも高くなります。
→解決事例を見る
-
(4)パイプは市場で流通している既成のサイズを活用する
【Before】
精密板金においては、市場に流通している規格品をうまく活用することで納期短縮とコスト削減に繋げることができます。例えば上記のようにパイプ形状の物を使用する場合、市場に流通していない太さのもので設計を行うと、ステンレスなどの板から三本ロールなどで曲げ加工を行なった上で溶接をしなければなりませんので、溶接の手間とコストがかかってしまいます。
→解決事例を見る
-
(5)目的とコストを勘案して表面処理方法を選択する
【Before】
鉄などの材質を使って精密板金の筐体製作する場合、防錆や外観向上を目的として塗装する場合が多くありますが、この塗装をどのように行うかによっても大きくコストが左右されます。例えば上記のように、精密板金で製作した筐体の外側に加えて内部まで塗装するような「全面塗装」を行うと、単純に塗装工程が倍になり、コストが割高になります。
→解決事例を見る
-
(6)塗装範囲を明確にしコストダウンを行う
【Before】
鉄などの材質を使って精密板金の筐体製作する場合、防錆や外観向上を目的として塗装する場合が多くありますが、この塗装をどのように行うかによっても大きくコストが左右されます。例えば上記のように、精密板金で製作した筐体の外側に加えて内部まで塗装するような「全面塗装」を行うと、単純に塗装工程が倍になり、コストが割高になります。
→解決事例を見る
-
(7)レザーサテンを採用し傷による歩留まり低下を回避する
【Before】
鉄系の素材を使用した精密板金を製作する際、外観を重視して塗装を施される場合があります。この塗装においても表面に光沢のあるもの、マットな仕上がりになるものなど様々な種類がありますが、通常の塗装方法であれば製品の出荷・梱包時、あるいは取扱い時に少しでも接触するとキズが入ったり異物が目立ちやすくなります。
→解決事例を見る
-
(8)パンチングメタルは市場で流通している既成のサイズを活用する
【Before】
規格表に無い、もしくは有ってもあまり流通していないパンチングメタルを使用する場合は、メーカーに依頼して特別に対応してもらう必要があります。メーカー品は値段も高く納期がかかります。また、1ロット500kg 以上を求められることもあり、 1、2枚といった小ロットでの対応はしてもらえません。穴が近すぎる・小さすぎるといったような要求が難しい場合も断られることがあります。
→解決事例を見る
-
アルミに化成処理を行うことより、傷を防ぎ、防錆性を向上させる
【Before】
アルミは軽量であり、加工性が高いことからあらゆる精密板金加工品で使用されています。その反面、アルミは非常に傷がつきやすいといった欠点もございます。実際に、当事例ではお客様よりアルミ製品への傷を防止したいとご相談がありました。さらに、RoHS指令への対応をご要望でした。
→解決事例を見る
-
SUS304からZAM材に材質変更しコストダウン
【Before】
精密板金で使用される主な材料のステンレス、アルミ、鉄などは、材料価格が高騰しています。 その中でも、特にステンレスの材料価格は2年前と比較すると、2倍近くまで上昇しています。 そのため、ステンレスの材料価格の高騰対策として、このSUS304の代替となる材質を上手に活用し、材料費の削減を図ることが非常に重要となります。
→解決事例を見る
-
SUS304からSUS430に材質変更しコストダウン
【Before】
精密板金で使用される主な材料のステンレス、アルミ、鉄などは、材料価格が高騰しています。 その中でも、特にステンレスの材料価格は2年前と比較すると、2倍近くまで上昇しています。 そのため、ステンレスの材料価格の高騰対策として、このSUS304の代替となる材質を上手に活用し、材料費の削減を図ることが非常に重要となります。
→解決事例を見る